Химические элементы, обладающие высоким сродством к кислороду (кальций, алюминий титан и др.), являются одновременно модификаторами, которые оказывают решающее влияние не только на формирование структуры стальной матрицы, но и на морфологию (форму и строение) неметаллических включений. Поэтому при раскислении одновременно протекают процессы очистки стали от неметаллических включений и изменения их морфологии благодаря модифицирующему действию химических элементов, являющихся сильными раскислителями и присутствующих в стали в связанном состоянии в сотых и тысячных долях процента.
Наиболее сильными раскислителями являются лантан, церий, гафний, за ними следуют кальций, цирконий, магний, алюминий, бор, титан и ванадий. Высокой раскислительной способностью обладает углерод при температурах более 1250° С. При этих температурах раскислительная способность углерода такая же, как у кремния, ванадия и марганца. В соответствии с законом распределения, возможно понижение кислорода при перемешивании жидкого металла со шлаком, имеющим низкую концентрацию оксида железа FeO.
По степени раскисленности (а не по содержанию Si) стали разделяются на спокойные (до 0,003% О2), полуспокойные (до 0,018% O2) и кипящие (до 0,035% O2). В спокойной стали весь растворенный кислород связан в оксиды и силикаты. Сера, имея большое сродство к марганцу, в низколегированной стали оказывается вся связанной в сульфиды марганца. При этом основная часть оксидов находится внутри сульфидов, являясь для последних центрами их образования. Поэтому при металлографических исследованиях на поверхности шлифов наблюдают преимущественно сульфиды и оксисульфиды. Расчеты Ю. А. Шульте подтверждают, что преобладающим видом неметаллических фаз в стали являются включения сульфидного происхождения. Морфология оксисульфидов зависит от их химического состава, который, в свою очередь, определяется раскислителями и модифицирующими элементами, использованными для обработки стали в ковше.
Преобладание тех или иных неметаллических включений в стали и их морфология зависят от сродства удаляемых из нее вредных примесей (S, Р, О, N) с элементами-раскислителями и модификаторами. Мерой сродства элементов является свободная энергия образования их соединений. И для всех них она падает с повышением температуры. В противоположность указанным элементам, раскислительная способность углерода с повышением температуры увеличивается. Поэтому углеродом можно восстанавливать все металлические оксиды, если температура процесса будет достаточно высокой.
Хорошо известно, что химические элементы, имеющие большое сродство к кислороду (т. е. сильные раскислители), как правило, имеют большое сродство к сере и по степени сродства располагаются в том же порядке. Поэтому перед десульфурацией содержание кислорода должно быть снижено до минимальных концентраций для того, чтобы химические элементы-десульфураторы и модификаторы не вступали с ним во взаимодействие. Авторы работы установили, что при десульфурации стали с содержанием 0,3 % С твердой известью содержание серы в ней можно снизить только до значений, равных шестикратной концентрации кислорода. Для достижения содержания серы 0,020% концентрация кислорода в металле должна быть ниже 0,0004%. Поэтому перед десульфурацией стали известью необходимо раскислить металл кремнием и алюминием или углеродом в процессе вакуумирования.
В низколегированных сталях, содержащих до 2% Мn, присутствуют в основном сульфиды марганца и в значительно меньшем количестве сульфиды железа. Последние образуют с железом по границам зерен эвтектику с низкой температурой плавления (около 985° С), которая часто является причиной красноломкости при температурах горячей прокатки. Присутствующий в стали марганец предупреждает красноломкость.
В сталях повышенной и высокой прочности усталостные трещины наиболее часто зарождаются в результате расслаивания поверхности раздела между матрицей и включением, в том числе глобулярной формы. Еще легче усталостные трещины образуются около неметаллических включений остроугольной формы. Высокие растягивающие напряжения, возникающие у концов микротрещин, вызывают их рост и слияние с соседними трещинами, что приводит к образованию полостей и к дальнейшему разрушению.
А. Б. Куслицкий и Г. М. Ицкович на основании результатов собственных исследований, а также на основании результатов обобщения и анализа экспериментов других специалистов пришли к выводу, что структура матрицы не является причиной разрушения металла. По их мнению, причиной разрушения стали является вид и морфология неметаллических включений, и поэтому концепция «чистой стали», не учитывающая роли неметаллических включений, является нереальной.
Различает три типа сульфидных включений: глобулярные (тип I), в виде цепочек (тип II) и многогранные (тип III). Образование сульфиде в I и II типов зависит от содержания кислорода в стали: при содержании кислорода более 0,02 % образуются глобулярные сульфиды типа I; при содержании кислорода в пределах 0,01-0,02% образуются сульфиды в виде цепочек по границам зерен (тип II) и одновременно небольшое количество сульфидов глобулярной формы (типа I); при содержании кислорода менее 0,01 % сульфиды выделяются только по границам зерен в виде цепочек (тип II). Сульфиды типа III имеют многогранную остроугольную форму и однородный химический состав — сульфид марганца (MnS). Сульфиды марганца образуются при определенном соотношении углерода, кремния и алюминия. Наиболее частые сочетания типов сульфидных выделений в стали (в порядке их преобладания): типы 1 и II и типы III и II. При этом сульфиды типа III образуются в низколегированной хорошо раскисленной кремнием и алюминием малоуглеродистой стали
Сопротивление сульфидов деформации при горячей прокатке различно и очень мало у сульфидов типа III. Максимальное сопротивление деформации при высоких температурах имеют глобулярные сульфиды типа I, которые практически не изменяют формы при горячей прокатке. Поэтому кипящая сталь СтЗкп характеризуется высокой ударной вязкостью при волокнистом изломе, однако переходит в хрупкое состояние при высоких температурах.
В работах исследованы влияние температуры и степени деформации на пластичность стальной матрицы и сульфидов типов I и III. Исследования проводили при температурах прокатки 800, 900, 1000, 1200° С. Анализ результатов позволяет сделать вывод, что при указанных температурах прокатки и при всех исследованных степенях деформации относительная пластичность сульфидов типа I значительно ниже, чем у стальной матрицы. При снижении температуры прокатки с 1200° С до 900° С пластичность сульфидов увеличивается и при 900° С достигает максимальных значений, затем начинает снижаться.
Относительная пластичность сульфидов типа III при снижении температуры прокатки увеличивается и уменьшается при увеличении степени деформации. При каждой температуре прокатки деформируемость сульфидов типа III намного выше, чем типа I, а при температуре 800° С она становится равной пластичности стальной матрицы.
Влияние температуры прокатки на деформацию сульфидов марганца типа II аналогично влиянию на сульфиды типа III, т.е. их деформируемость повышается при снижении температуры прокатки до 800° С и ниже. Увеличение длины сульфидов марганца типа II сокращает расстояние между скоплением включений, что облегчает распространение трещин.
Результаты исследований показывают, что наиболее благоприятной температурной областью прокатки стали, в которой присутствуют сульфиды типа I (кипящая сталь), является температура около 900° С.
Особенности поведения сульфидов типов II и III при пониженных температурах горячей прокатки (850° С и ниже) свидетельствуют о необходимости максимально возможной очистки от них стали, подвергаемой контролируемой прокатке. Следует отметить, что при умеренном содержании в стали неметаллических включений управление их морфологией при модифицировании с целью глобулизации и повышения сопротивления деформации при температурах горячей обработки так же важно, как и дальнейшее снижение содержания серы. Снижение содержания серы до 0,005 % и менее является до настоящего времени технически сложной задачей, требующей специального оборудования, и не всегда экономически оправдано.
Раскисление стали и морфология сульфидных включений
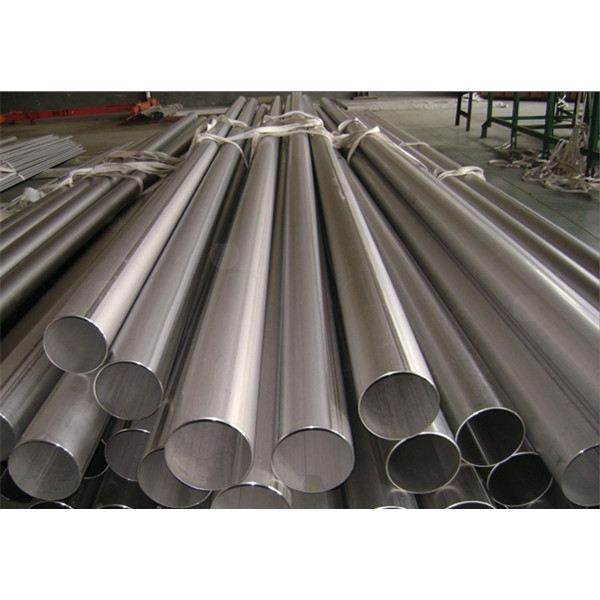
- 05/12/2013
- 5784 views
Раскисление металла является одним из важнейших технологических звеньев при производстве стали требуемого качества.