Статистический анализ сталей высокой прочности показал, что металл, поступающий с металлургических предприятий, в большинстве случаев, удовлетворяет заданным требованиям лишь после улучшения.
В Австрии и Японии производят термически улучшаемый прокат из кремнемарганцовистых сталей, содержащих (менее) 0,18% С; 1,5% Мn и 0,5% Si. Стали такого типа всесторонне исследованы и в нашей стране. Стандарты предусматривают поставку термически улучшенных кремнемарганцовистых сталей марок 10Г2С1, 09Г2С, 14Г2. 17ГС и т. п. Наиболее перспективны для использования в сварных конструкциях стали с малым содержанием углерода. Так, например, у термически улучшенного проката из сталей, содержащих 0,09-0,12% С; 1,3-1,65% Мn и 0,7-0,9% Si. Получение высокой прочности термически улучшаемых кремнемарганцовистых сталей обусловлено легкостью формирования в прокате развитой субструктуры. Прокат из этих сталей весьма однороден. Закаленные и высокоотпущенные кремнемарганцовистые стал обладают высоким сопротивлением зарождению и распространению трещин. Особенно хорошие результаты обеспечивает применение стали содержащей 0,09-0,012% С; 1,3-1,65% Мn; 0,7-0,9% Si. Прокат из стали такого химического состава по сравнению с другими низколегированными сталями имеет наиболее высокий уровень K1c. Изучение свариваемости термически улучшаемой стали 10Г2С1 в прокате толщиной до 40 мм, выполненное А. Я. Бродским и Н. В. Толмачевой, включало определение оптимальной погонной энергии дуги, склонности предварительно наклепанной стали к старению в зоне термического влияния (ЗТВ), локальных изменений предела текучести и ударной вязкости стали в ЗТВ сварного стыкового соединения, склонности стали в ЗТВ к хрупким разрушениям при наличии естественных и искусственных концентраторов напряжений. Кроме того, исследовали механические свойства металла шва сварного соединения. Было установлено, что температура порога хладноломкости предварительно деформированной стали в зоне термического влияния на участке старения составляет -60° С. Зона разупрочнения стали по пределу текучести распространяется примерно на 40 мм от оси шва. Однако локальные значения предела текучести на разупрочненном участке сварного соединения и зоны термического влияния не опускаются ниже гарантированного значения (400 Н/мм2) для исходной стали; иными словами, рассматриваемый прокат не разупрочняется при сварке. В целом был сделан вывод о хорошей свариваемости исследуемой стали. При скорости охлаждения зоны термического влияния, равной 4-18° С/с, ударная вязкость и предел текучести стали 10Г2С1 практически не снижаются.
Нормативными документами термически улучшаемые кремнемар-ганцовистые стали рекомендованы для ответственных строительных конструкций. Эти стали дешевы, не содержат дефицитных легирующих элементов, имеют гарантированный предел текучести σт ≥ 400 Н/мм2; они, по-видимому, являются наиболее перспективными сталями для изготовления строительных конструкций широкого назначения.
Особенно эффективно применение стали 15ХСНД для конструкций, работающих при расчетной температуре ниже -40° С (в главных пролетных строениях мостовых конструкций, в тяжелонагруженных узлах транспортеров и других особо ответственных конструкциях). В конструкциях же широкого назначения, особенно эксплуатируемых в районах с расчетной температурой выше —40° С, предпочтение следует отдавать кремнемарганцовистым сталям.
В настоящее время, когда на первый план выходят вопросы качества проката и современная экономика учитывает этот факт, сталь 10ХСНД с повышенной атмосферной стойкостью стала широко применяться при строительстве ответственных конструкций. Ее использовали при изготовлении уникальных зданий в Москве, возводимых к 850-летию города, прежде всего в конструкциях покрытия Большой спортивной арены (БСА) стадиона в Лужниках. Эта сталь была микролегирована ванадием и ниобием для полного связывания азота, находящихся в твердом растворе. Учитывалось, что плавки проводили в электропечах, где содержание азота достигает 0,012 %. Считается, что азот будет связан полностью при выполнении соотношения Nэ = 0,8[0,52Аl + 0,29Ti + 0,27V + 0,5Nb], где N3 — азот, связанный в нитриды (карбонитриды); Al, Ti, V, Nb — содержание элементов, %. Следует отметить, что прокат из стали 10ХСНД имел высокую чистоту по вредным примесям и газам, отвечал всем высоким требованиям, предъявляемым к прокату из нее, и поэтому фактически относится к прокату нового поколения σT≥ 400 Н/мм2.
Особенно следует указать на неизмеримо более высокую ударную вязкость современных сталей по KCV-40. Фактически ранее выпуск проката с этой характеристикой не удавался.
Следует также обратить внимание на низкий углеродный эквивалент Сэ, который должен способствовать высокому сопротивлению хрупким разрушениям сварных соединений.
Поскольку свариваемость низколегированных сталей ухудшается с увеличением толщины проката, некоторые характеристики были специально исследованы на прокате с максимальной толщиной, равной 40 мм. Испытания проводили методом валиковой пробы. Поскольку сварку стали следовало вести по наиболее жестким стандартным режимам, в соответствии с действующими нормами выбирали минимальный размер катета шва: для проката толщиной 40 мм стали данной прочности минимальный катет равен 9 мм. Для выполнения такого шва тепло-вложение должно составлять q/v = 32,5 кДж/см. Наплавку вели в паз размерами 2 х 4 мм электродами УОНИ 13/55 диам. 6 мм.
Твердость околошовной зоны измеряли методом Виккерса; замеры проводили через 2 мм, при этом максимальная твердость достигала НУ 250. Поскольку в случае HVmax < HV 320 опасность образования холодных трещин исключается, полученный результат весьма высок. Все же, учитывая большую толщину проката, при сварке на монтаже применяли предварительный подогрев. Тем более, что согласно действующим нормам сталь с σT > 390 Н/мм2 сваривается (в рассматриваемых толщинах) без предварительного подогрева при температурах не ниже 0° С, а монтаж конструкций проводили при отрицательной температуре.
Для оценки сопротивления металла околошовной зоны хрупким разрушениям проводили испытания на ударный изгиб образцов с острым Т-образным надрезом. При этом, как и положено при валиковой пробе, надрез располагали параллельно поверхности проката. Вершина надреза совпадала с линией сплавления, где, как известно, наблюдается минимальная ударная вязкость у сталей рассматриваемого типа. Испытания проводились в интервале температур от нормальной до —60° С. Оценивали ударную вязкость (KCV), относительное сужение у дна надреза, а также количество волокна в изломе (В).
Наконец, испытания показали, что z-свойства проката также достаточно велики: Ψz ≥ 15 %, что для конструкции данного сооружения вполне достаточно.
Из приведенных в разделе данных видно, что выпускаемый в настоящее время в нашей стране прокат из сталей высокой прочности по уровню сопротивления хрупким разрушениям не уступает лучшим сортам аналогичного зарубежного проката.
Термически улучшенные стали
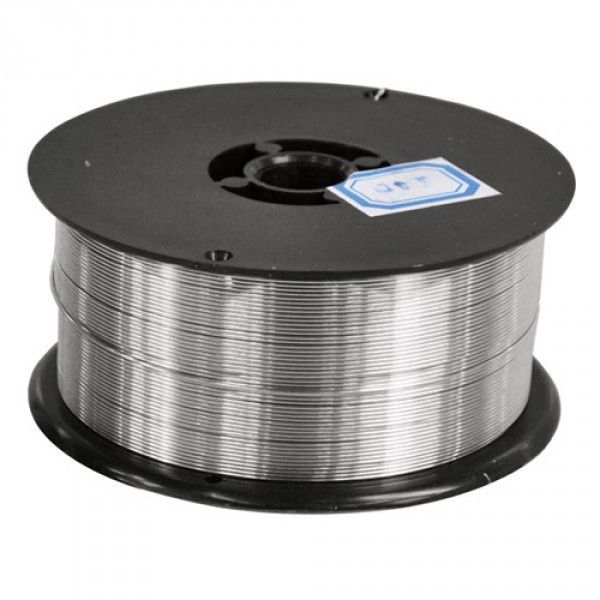
- 05/12/2013
- 3613 views
Термическое улучшение малоуглеродистых низколегированных сталей массового назначения