Проследим, какую роль играют механизмы упрочнения в сталях для строительных конструкций. Авторы работы отмечают, что в низколегированных сталях воздействие на прочностные характеристики отдельных механизмов упрочнения можно считать аддитивным.
Расчет вклада отдельных упрочняющих факторов в предел текучести или предел прочности выполняется методами линейного многофакторного регрессионного анализа с помощью стандартной программы. При таком подходе все независимые переменные могут быть найдены химическими или металлографическим методами.
Доминирующим фактором, определяющим вид диаграммы растяжения низкоуглеродистых сталей с площадкой текучести, является наличие зерен феррита. Дисперсная фаза оказывает, в основном, количественное влияние, позволяя получить на феррито-перлитных сталях уровень предела текучести σт = 400...500 Н/мм2.
В зависимости от марки стали и способа охлаждения в прокате формируется микроструктура различной морфологии — игольчатый феррит, бейнит различного строения, мартенсит. В соответствии с этим прочность закаленной стали может изменяться в широких пределах (от 600 до 1500 Н/мм2). Закаленные стали характеризуются высоким коэффициентом деформационного упрочнения; он существенно выше, чем у сталей с феррито-перлитной структурой, и колеблется в широких пределах. Однако имеется коренное отличие работы под нагрузкой закаленных сталей и сталей с феррито-перлитной структурой: у закаленных сталей на диаграмме σ—ε отсутствует площадка текучести.
Кроме того, разница между σ0,2 и σ0,01 у закаленных сталей весьма значительна — 100...300 Н/мм2, что не позволяет рационально использовать полученный в этих сталях уровень прочности в сжатых и сжато-изогнутых элементах конструкций. В работе достаточно подробно рассмотрены причины различий в прочности сталей, отличающихся друг от друга по химическому составу и режимам термического упрочнения. На прочность закаленных сталей влияют величина зерна (размер мартенситных игл), упрочнение феррита легирующими элементами, плотность дислокаций, количество растворенного углерода, дисперсные карбиды, выделившиеся непосредственно при γ —α-превращении или при самоотпуске мартенсита.
Повышение прочности сталей 10Г2С1 и 14Г2 по сравнению со сталью Ст3 связано, в основном, с ростом Более высокую прочность стали 15Г2СФ по сравнению с прочностью стали 14Г2 можно объяснить более мелким зерном и наличием специальной карбидной фазы, оставшейся нерастворенной при аустенитизации. Иными словами, в рассматриваемом случае увеличение прочности происходит, в основном, в результате роста второго и третьего членов в уравнении.
Повышение прочности горячекатаной и нормализованной стали 15Г2СМФР объясняется спецификой морфологии глобулярного бейнита с островками мартенсита. Неполнота промежуточного превращения приводит к сохранению определенной доли не превращенного аустенита, обогащенного углеродом, который при охлаждении может превратиться в мартенсит. Наличие таких островков приводит, по данным работы, к увеличению σ0,2 и σВ примерно на 100 Н/мм2, что и наблюдается в рассматриваемом случае. Дальнейшее увеличение прочности закаленной стали 15ХГ2СМФР объясняется ростом а0 и действием дисперсных частиц.
В закаленных сталях также можно выделить доминирующий механизм упрочнения, объясняющий не только повышение прочности охлажденных в воде низколегированных сталей, но и специфический вид их диаграмм напряжение—деформация. Таким механизмом является действие высокой плотности неупорядоченных дислокационных сеток, заблокированных в определенной степени атомами углерода и дисперсными карбидами. Отсутствие площадки текучести на диаграмме а—е можно объяснить и другими явлениями — неоднородностью локальной прочности при закалке, наличием остаточного аустенита и т.д. Доминирующее влияние высокой плотности дислокационных сеток отчетливо наблюдается пои анализе сопротивления закаленных сталей хрупким разрушениям; такие стали всегда хрупки и хладноломки, что и должно быть при рассматриваемом механизме упрочнения. Измельчение зерна или введение в сталь никеля в этих условиях недостаточно эффективно.
Таким образом, механизм упрочнения дислокациями высокой плотности, как доминирующий, непригоден для создания сталей высокой прочности.
При высокотемпературном отпуске закаленных сталей происходит формирование субзерен. В целом такую микроструктуру можно идентифицировать как сорбит отпуска, в котором процессы полигонизации и рекристаллизации ферритной матрицы прошли достаточно полно. Кроме того, в сталях, легированных сильными карбонитридообразуюшими элементами, г микроструктуре содержится дисперсная карбонитридная фаза.
Достижение уровня класса прочности С390 у сталей типа 10Г2С1 и 15ХСНД связано с измельчением микроструктурных составляющих, в первую очередь с формированием субзерен. По этой же причине, по-видимому, происходит дополнительное увеличение прочностных характеристик термически улучшенных сталей с нитридным (карбонитридным) упрочнением (по сравнению с нормализованными). Обеспечение же уровня класса прочности С590 и выше в сложнолегированных сталях объясняется, вероятно, дополнительным упрочнением в результате некоторого повышения плотности дислокаций, которое имеет место из-за более высокого сопротивления отпуску сталей, закаливаемых на мартенсит.
Таким образом, для высокоотпушенных термически улучшенных строительных сталей доминирующим является субзеренный механизм упрочнения; это приводит не только к увеличению прочности стали, но и к повышению сопротивления ее хрупким разрушениям.
Упрочнение низколегированной стали
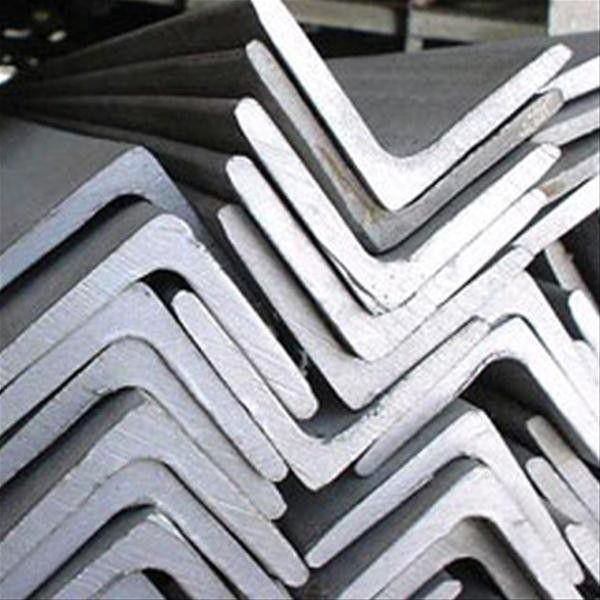
- 05/12/2013
- 4102 views
Приведенные выше данные показывают, что различные механизмы упрочнения строительных сталей обусловливают неодинаковое поведение проката под нагрузкой.